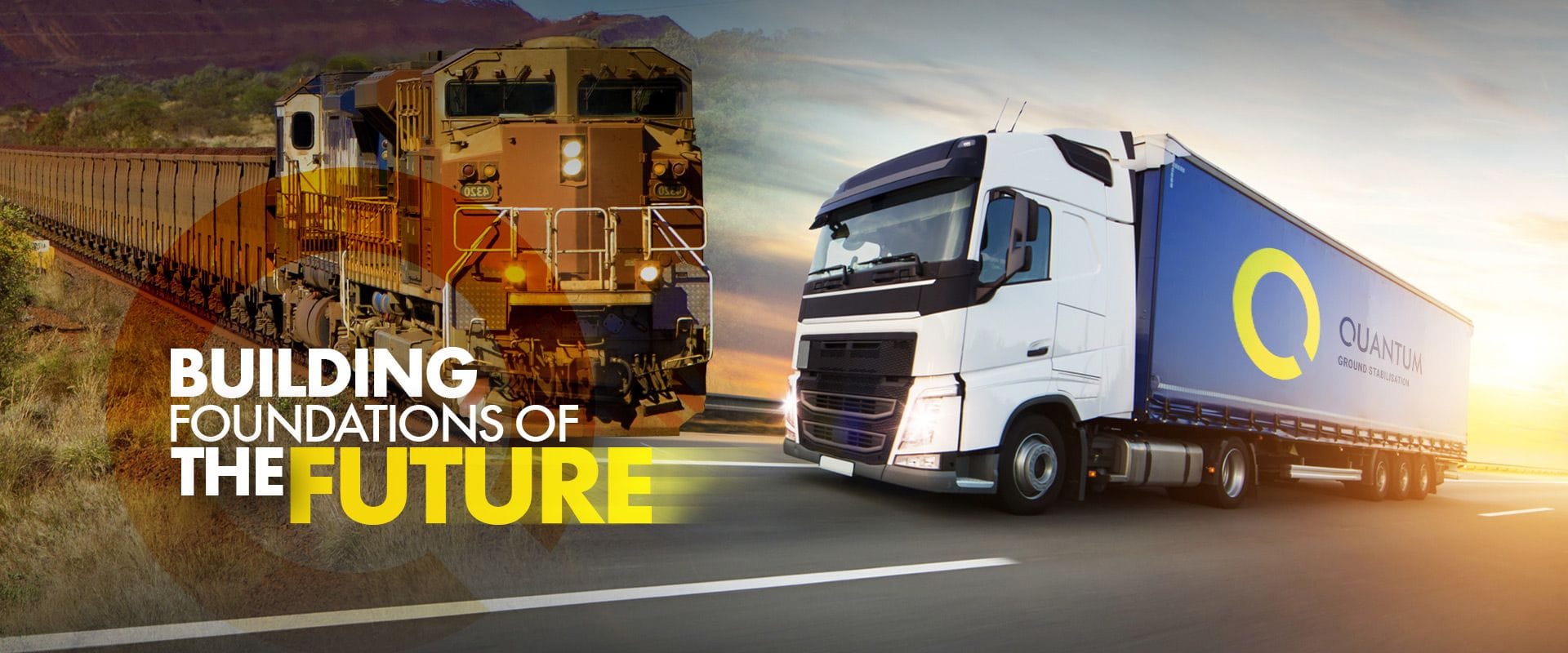
Laboratory Mix Design Process
Background
The calculations included in the “Soil Additive Calculations” spreadsheet are based on the following field guidance provided by Quantum Ground Stabilisation Pty Ltd for treating materials with Quantum Powder Formulation (QPF) and Quantum Liquid concentrate (QLC) additives.
Note: The Quantum ready to use (RTU) liquid additive is the dilute form of the Quantum Liquid concentrate (QLC), the active ingredient, which is diluted at the ratio of one part to four parts water.
“In 95 to 98% of all cases the standard quantities of the RTU liquid additive and the QPF product will yield the desired effect. Only in very few and rare cases it may be necessary and advisable to adapt the dosage. For this purpose, simple laboratory tests are conducted, a point which is being discussed below.
Generally, the Quantum ready to use (RTU) liquid additive is mixed with the soil to a depth of 25 cm, and a standard quantity of 0.25 litres per m2 or 1 litre per m3 is recommended in 95 to 98 out of 100 cases.The upper 10 cm of this layer already treated with the RTU liquid product receives an additional treatment with the QPF product. The standard quantities for the QPF product are between 2 and 4 kg per m2.”
Note: TMR has indicated it will apply both the RTU liquid additive and QPF dry additive to a depth of 250 mm.
Preliminary testing
Select a host material
Undertake the following testing on the selected host material:
- Particle size distribution in accordance with Q103A Particle size distribution of soil - Wet sieving
- Atterberg Limits in accordance with Q104A Liquid limit of soil, Q105 Plastic limit and plasticity index of soil, Q106 Linear shrinkage of soil
- Moisture/density relationship using standard compaction in accordance with Q142A Dry density-moisture relationship of soils and crushed rock - standard
Determine the quantity of additives (dry and liquid)
- Volume of the RTU liquid additive applied in the field = 0.25 L/ m2 to a depth of 250 mm
Calculate the dry QPF additive mass (based on stabilisation to 250 mm depth) (normally for a 100 mm layer)
The typical field spread rate of the dry QPF additive range between 2 - 4 kg/m2 for a 100 mm stabilisation depth. This is equivalent to 5 - 10 kg/m2 for a 250 mm stabilisation depth
Key to achieving an optimal dosage rate is to prepare samples at the nominated low, medium and high dry QPF additive contents at a fixed liquid additive dosage.
Use the “Soil Additive Calculations” spreadsheet to translate the following dosage rates for a 250 mm thick layer:
RTU liquid additive L/m2 to L/m3
Dry QPF additive (powder) kg/m2 to % by mass of host material
HOLD POINT - Check the dry QPF and RTU liquid additive calculations and confirm with Quantum Ground Stabilisation Pty Ltd for confirmation that additive amounts are correct.
This translation will allow the values to be used in standard calculation processes in test method Q135A.
UCS testing
Standard sample preparation
- Q101 Preparation of disturbed samples Testing using the standard methods below:
- Q115 Unconfined compressive strength of stabilised materials
- Q251A Preparation and compaction of laboratory mixed stabilised materials
- Using MDD/OMC of host material
Q145A Laboratory compaction to nominated levels of dry density and moisture content
- Q135A Addition of stabilising agents
- dry QPF additive (powder added first)
- RTU liquid additive diluted in mixing water
- Q135B Curing moulded specimens of stabilised material
- Curing for 7 and/or 28days as requested
The Materials Testing Manual (MTM) provides methods (Q documents) for sampling and testing of soils, aggregates, rocks, bituminous materials, asphalt, concrete and pavements:
Additional information
Has the target 28-day UCS value of between 1 - 2 MPa been met?
Can mix design requirements be achieved with a dosage rate of 2, 3 or 4 kg/m2? If a 1 MPa UCS cannot be achieved with the maximum dosage rate of 4 kg per m2, then this stabilisation method is not suitable for the host material.
It is also important to assess the working time of the material in accordance with Q136A Working time of stabilised material, to determine the maximum length of time between mixing of materials with stabilisation additives and compaction.
For explanations DTMR ref. numbers, please search reference numbers from your favourite search engine
Researcher: Dr James Grenfell Australian Road Research Board